JBR Plastic Injection Mold Design and Development stands out
With many years of experience in Mold Design and Development, mold making, plastic injection molding manufacturer, leading technical solutions and perfect quality service in JBR. JBR (JinBaoRong)Precision Industry Product Co., Ltd is a mold design and development manufacturer, that specializes in injection mold design and has helped many industries manufacture top-quality products. Also we have rich expierences on die casting mold design.
JBR Molds boasts seasoned engineers in plastic injection molding, dedicated to efficient design and manufacturing. Our injection molds are crafted with exceptional precision and tight tolerances, ensuring a seamless match with the geometric shapes of your part designs. We firmly believe that molds should deliver long-term value. That’s why we advocate for high-quality, durable materials that serve you through countless production cycles. Trust JBR Molds for injection molds that prioritize accuracy, longevity, and enduring performance.
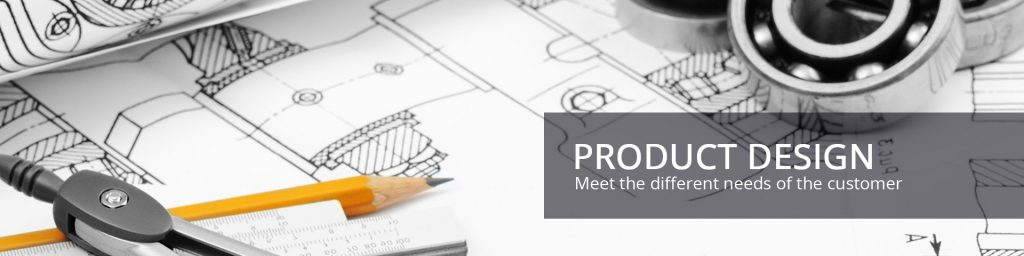
Plastic product design and tooling design development services including injection mold design and die casting mould services. Plastic Resin Materials handled include acetal, acrylic, ABS, ASA, polyester, polyimide, polymethyl pentene, polyolefin, polypropylene, polystyrene, polyvinyl chloride, thermoplastic polyurethane, thermoplastic elastomers and polyethylene; metal including Aluminum, Zinc and Magnesium alloy.
Capabilities include contract manufacturing, plastic and medical injection molding, compression molding, spare tooling, injection mold tooling, machining, precision tooling, milling, decorating, packaging, assembly, manufacturing, pad printing, rapid prototyping, milling, drilling, heat staking, sonic welding and laser-etching. Mold design services are available for medical device, pharmaceuticals, telecommunications, industrial and transportation, consumer and business applications. Meet FDA standards.
1. Injection Mold Gate Design
The casting system of injection molding molds plays a pivotal role in both mold production and product quality. The rationality of gate design directly influences the quality of the product, encompassing aspects such as appearance, warpage, weld lines, flow marks, and trapped air. At JBR, our experienced engineers understand the critical importance of an intelligently designed gating system to achieve optimal results in product aesthetics and structural integrity.
2. Injection Mold Cooling System Design
A well-designed cooling system can significantly reduce molding cycles, enhance production capacity, and lower costs. Conversely, inadequate cooling system design can prolong molding times, leading to increased costs and uneven cooling that results in defects such as warpages. Our meticulous approach to cooling system design at JBR Molds ensures efficiency, reliability, and uniform cooling, mitigating the risk of undesirable product deformities and ensuring optimal manufacturing performance.
3. Injection Molding System Design
The design of the molding system holds sway over both mold manufacturing and injection cycles, as well as the final appearance and performance of the product. Our engineers at JBR Molds devote meticulous attention to the design of cores and cavities, ensuring an optimized molding system that guarantees the delivery of top-notch products. By focusing on precision and functionality, we strive to surpass industry standards in molding system design, thus assuring the best possible outcomes for our clients.
4. Ejection System Design
The ejection system is a critical determinant of the final product’s appearance and performance. An imprudent ejection system can lead to issues such as deformation, whitening, and cracking. With over 30 years of mold design experience, we at JBR Molds bring our expertise to bear, ensuring a well-thought-out ejection system that enhances the overall quality of the molded products. Trust us to deliver molds that not only meet but exceed your expectations, providing solutions that stand the test of time.
Mold design and development is a crucial aspect of manufacturing processes, especially in industries like plastics, rubber, ceramics, and metalworking. A mold is a hollow form typically made of metal into which molten material is poured or pressed to create a desired shape when cooled and solidified. Here’s an overview of the process:
Conceptualization:
It starts with understanding the requirements of the part to be produced. This includes its dimensions, material properties, quantity, and desired surface finish.
Mold design and development:
Based on the part specifications, engineers create a mold design using computer-aided design (CAD) software. This involves detailing the cavity, core, gating system, cooling channels, and ejection mechanism.
Mold design and development Material Selection:
The choice of mold material depends on factors like the material to be molded, expected production volume, and budget. Common materials include steel, aluminum, and various alloys.
Manufacturing:
Once the design is finalized, the mold is manufactured using machining processes such as milling, turning, grinding, and electrical discharge machining (EDM). Precision is critical to ensure the mold’s dimensions match the design.
Surface Treatment:
The mold surfaces may undergo treatments like polishing, texturing, or coating to enhance durability, surface finish, and release properties.
Testing and Iteration:
Before mass production, the mold undergoes testing to ensure it produces parts that meet quality standards. Any issues identified during testing are addressed through iterative design improvements.
Production:
Once the mold is validated, it’s ready for mass production. Molten material is injected, poured, or pressed into the mold cavity, allowed to cool and solidify, and then ejected to produce finished parts.
Maintenance:
Regular maintenance is crucial to prolong the mold’s lifespan and ensure consistent part quality. This includes cleaning, inspection, and repair of any wear or damage.
Throughout the mold design and development process, collaboration between design engineers, mold makers, material specialists, and manufacturing personnel is essential to achieve optimal results. Continuous improvement efforts help refine the process and optimize efficiency and quality.